Is your industry underestimating the power of nitrogen generators? Many businesses miss out on the cost savings, efficiency, and reliability that these devices bring. Nitrogen generators work by isolating nitrogen from other elements in the air, providing high-purity gas essential for diverse industrial applications. This article delves into understanding nitrogen generators, their operational principles, applications, benefits, costs, and maintenance requirements. Equip yourself with the knowledge to make an informed decision about integrating this efficient solution for your industry’s needs.
Understanding Nitrogen Generators
Nitrogen generators produce nitrogen gas by separating nitrogen from other elements like oxygen and carbon dioxide in the air. They provide a continuous supply of nitrogen, which is essential for various industrial applications. This process is both efficient and cost-effective, eliminating the need for high-pressure gas cylinders.
Pressure Swing Adsorption (PSA) nitrogen generators use columns packed with carbon molecular sieves (CMS) to trap smaller compounds and allow larger nitrogen molecules to pass through. This process can achieve nitrogen purity levels up to 99.999%. The CMS selectively adsorbs oxygen and other impurities when pressurised with air, and then releases them when the pressure is reduced, making it possible to produce high-purity nitrogen.
Membrane nitrogen generators work by filtering compressed air through hollow fibres. These fibres selectively permeate oxygen, water vapour, and other gases faster than nitrogen, allowing nitrogen to be separated and collected. Membrane generators can achieve nitrogen purity levels ranging from less than 90% to 99.9%. This method is advantageous for applications requiring lower to medium purity levels and where simplicity and low maintenance are priorities.
- Purity Levels: PSA can achieve up to 99.999%, while membrane generators range from <90% to 99.9%.
- Operational Complexity: PSA systems are more complex due to the use of CMS columns.
- Maintenance: Membrane systems typically require less maintenance compared to PSA.
- Application Suitability: PSA is ideal for high-purity applications; membrane is suited for lower purity needs.
- Energy Consumption: PSA systems generally consume more energy compared to membrane systems.
Applications of Nitrogen Generators
Nitrogen generators are integral to various industries due to their reliability and cost-effectiveness. They provide a continuous supply of nitrogen, eliminating the need for high-pressure gas cylinders and ensuring operational efficiency across different sectors.
In the electronics and rapid prototyping industries, nitrogen generators play a crucial role. They are used to create an inert atmosphere that prevents oxidation during the manufacturing process. This is particularly important in soldering and reflow processes, where the presence of oxygen can cause defects in electronic components. The consistent supply of high-purity nitrogen ensures the quality and reliability of electronic products.
The food packaging industry heavily relies on nitrogen generators for modified atmospheric packaging (MAP) and controlled atmospheric storage (CAS). These techniques extend the shelf life of perishable goods by replacing oxygen with nitrogen, which slows down the oxidation and spoilage processes. Nitrogen generators enable food manufacturers to maintain the freshness and quality of their products while reducing waste.
In laser cutting, nitrogen generators provide a dry, inert gas that prevents oxygen from interfering with the cutting process. This results in cleaner cuts and reduces the risk of oxidation, which can weaken the material. Additionally, nitrogen generators are used for tyre inflation to maintain consistent pressure and increase the lifespan of tyres. Nitrogen-inflated tyres experience less pressure fluctuation and are less prone to oxidation, leading to improved performance and safety.
Industry | Application |
Electronics | Creating an inert atmosphere during manufacturing processes |
Food Packaging | Modified Atmospheric Packaging (MAP) and Controlled Atmospheric Storage (CAS) |
Laser Cutting | Providing a dry, inert gas to prevent oxidation |
Tyres | Maintaining consistent pressure and increasing tyre lifespan |
Benefits of Using Nitrogen Generators
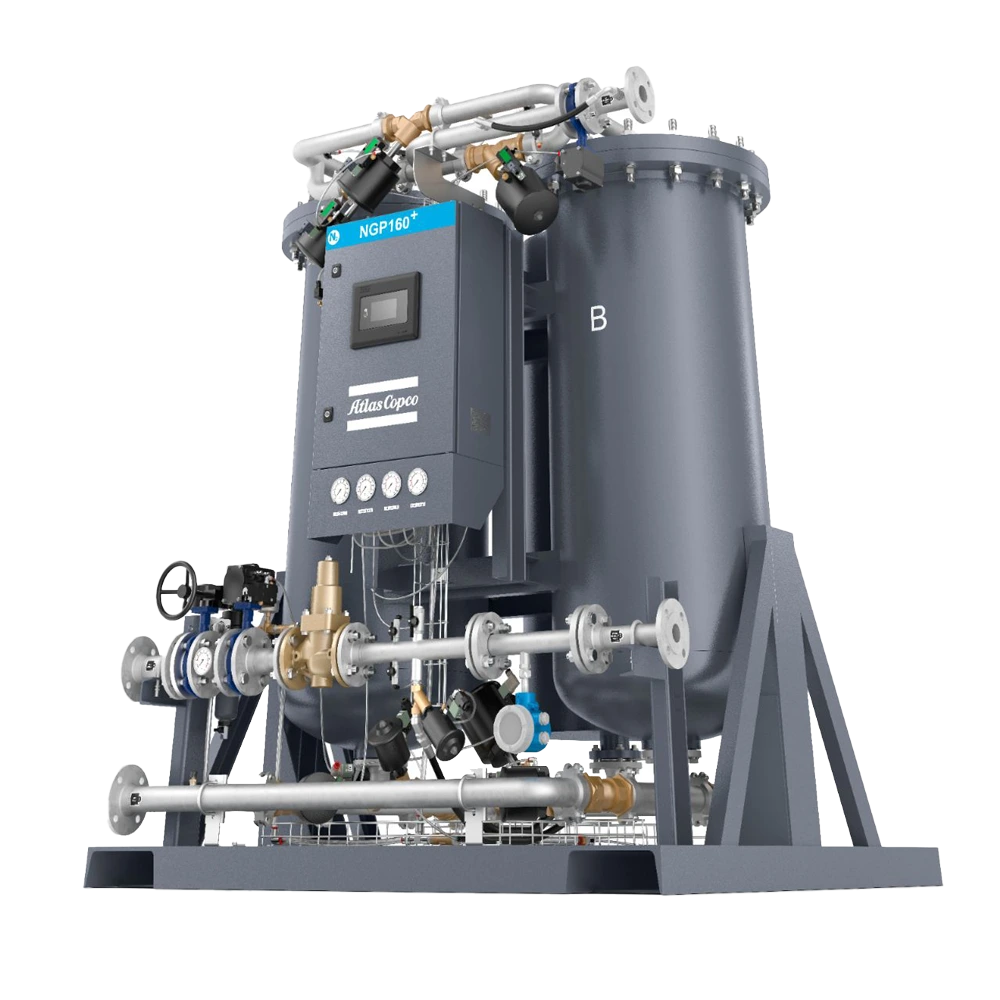
Nitrogen generators offer a range of benefits that make them an attractive solution for industrial applications. The key advantages include enhanced safety, significant cost savings, increased reliability, and improved performance. These benefits collectively contribute to the overall efficiency and effectiveness of industrial operations.
One of the primary benefits of nitrogen generators is safety. By eliminating the need for high-pressure gas cylinders, they reduce the risks associated with handling and storing compressed gases. This not only enhances workplace safety but also simplifies operational processes. Additionally, nitrogen generators offer substantial cost savings. Since there is no need to purchase and replace gas cylinders, maintenance costs are minimal, and the ongoing expenses are limited to the electrical energy required for operation. This makes nitrogen generators a cost-effective solution for continuous nitrogen supply.
Reliability is another significant advantage of nitrogen generators. They provide a continuous and consistent supply of nitrogen, preventing operational downtime caused by running out of gas. This is particularly important in industries where uninterrupted nitrogen supply is critical for maintaining production quality. The performance benefits of nitrogen generators are also noteworthy. They offer high throughput and consistent nitrogen purity, ensuring that industrial processes are carried out efficiently and effectively.
- Enhanced Safety: No high-pressure gas cylinders needed.
- Cost Savings: Minimal maintenance and no gas cylinder changes.
- Increased Reliability: Continuous nitrogen supply prevents downtime.
- Improved Performance: High throughput and consistent nitrogen purity.
Different Types of Nitrogen Generators
Nitrogen generators come in two main types: Pressure Swing Adsorption (PSA) and membrane nitrogen generators. Both systems have unique operational principles and are suited for different applications based on their efficiency, purity levels, and maintenance requirements.
PSA nitrogen generators use columns filled with carbon molecular sieves (CMS) to adsorb impurities such as oxygen and carbon dioxide. When air is pressurised, these sieves trap smaller molecules, allowing larger nitrogen molecules to pass through. This process can achieve nitrogen purity levels of up to 99.999%. PSA generators are particularly useful in industries where high-purity nitrogen is essential, such as electronics manufacturing and pharmaceutical production. The cyclic nature of PSA systems ensures a continuous supply of nitrogen, making them reliable for critical applications.
Membrane nitrogen generators operate by filtering compressed air through hollow fibre membranes. These fibres selectively permeate oxygen, water vapour, and other gases faster than nitrogen, enabling the separation and collection of nitrogen. Membrane generators can achieve nitrogen purity levels ranging from less than 90% to 99.9%. They are advantageous for applications requiring lower to medium purity levels, such as food packaging and tyre inflation. The simplicity and low maintenance of membrane systems make them an attractive option for industries prioritising ease of operation and cost-efficiency.
- Young In Chromas Tower Plus: A PSA nitrogen generator providing up to 99.999% purity.
- Young In Chromas Mistral Evo: Another PSA model known for its high efficiency and reliability.
- Young In Chromas Whisper: A membrane nitrogen generator offering purity levels from <90% to 99.9%.
Cost of Nitrogen Generators
Initial costs for nitrogen generators can vary considerably, typically ranging from $5,000 to $40,000. The price depends on the generator’s capacity, technology (such as PSA or membrane), and specific industry requirements. Investing in a nitrogen generator can be cost-effective in the long run, especially for businesses with a consistent demand for nitrogen.
Ongoing costs primarily involve the electrical energy required to generate the compressed air supply. Maintenance expenses are relatively low compared to the recurring costs of traditional nitrogen delivery methods. Regular maintenance tasks include checking for leaks, replacing filters, and ensuring the compressor is functioning optimally. These maintenance activities ensure the generator operates efficiently and prolongs its lifespan.
The cost-saving benefits of nitrogen generators are significant. By generating nitrogen on-site, businesses eliminate the need for frequent gas cylinder replacements and deliveries, reducing operational downtime. This continuous supply of nitrogen ensures that production processes are uninterrupted, enhancing overall efficiency. Additionally, on-site generation reduces the environmental impact associated with the transportation and handling of high-pressure gas cylinders.
- Initial Investment: Varies from $5,000 to $40,000 based on capacity and technology.
- Energy Consumption: Ongoing costs mainly involve the electrical energy for compressed air supply.
- Maintenance: Low maintenance costs compared to traditional nitrogen delivery.
- Operational Efficiency: Continuous nitrogen supply eliminates downtime and reduces operational costs.
Maintenance of Nitrogen Generators
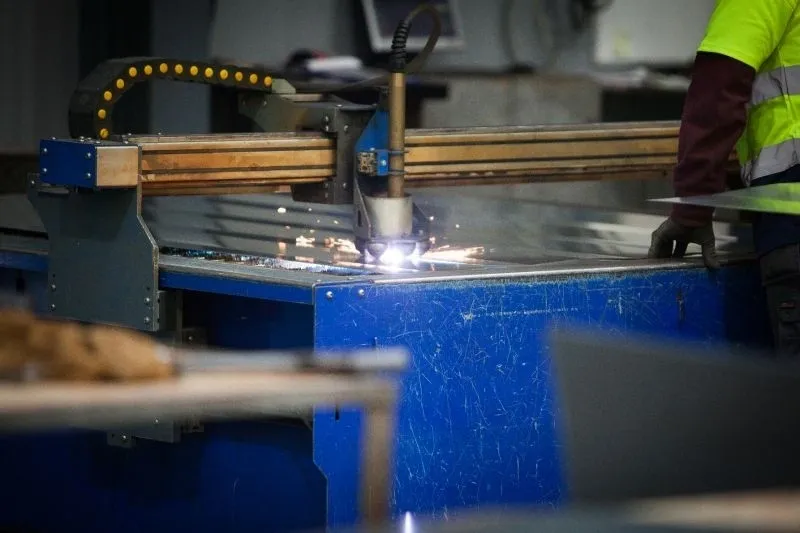
Regular maintenance of nitrogen generators is crucial for their optimal performance and longevity. Proper upkeep not only ensures a continuous supply of high-purity nitrogen but also enhances the safety and efficiency of industrial operations. Neglecting maintenance can lead to equipment failure, increased operational costs, and potential safety hazards.
Key maintenance tasks for nitrogen generators include checking for leaks, replacing filters, and ensuring the compressor is functioning optimally. Leaks can result in reduced nitrogen purity and increased energy consumption. Filter replacement is essential to prevent contaminants from entering the system and compromising the quality of the nitrogen produced. The compressor, being a vital component, needs regular inspection and servicing to maintain efficient performance.
Portable nitrogen generators require similar maintenance but with additional considerations due to their mobility. Regular inspection for wear and tear caused by transportation is necessary. Ensuring that portable units are securely mounted and protected during movement can prevent damage. Additionally, portable generators may require more frequent filter changes and leak checks due to the varying conditions they operate in.
- Check for Leaks: Regularly inspect for and repair any leaks to maintain efficiency.
- Replace Filters: Change filters according to the manufacturer’s recommendations to ensure high nitrogen purity.
- Inspect Compressor: Conduct routine checks and servicing of the compressor for optimal performance.
Final Words
In the action, this article explored the essential aspects of nitrogen generators, emphasising their operational principles, diverse applications, and significant benefits.
Nitrogen generators offer reliable, cost-effective solutions across multiple industries, from electronics to food packaging. By detailing PSA and membrane generators, the article highlighted the efficiency and performance these systems provide.
Understanding the costs, types, and maintenance of nitrogen generators is crucial for businesses seeking to optimise their operations.
Ultimately, nitrogen generators stand out for their safety, high purity, and continuous supply, making them indispensable in modern industry.
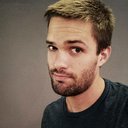
Barnaby is a music journalist specializing in pop music trends, artist spotlights, and album reviews. He focuses on exploring the creative processes behind chart-topping hits and providing fresh insights into the evolving pop music landscape.